Rheology Basics and Testing Rheological Properties
Rheological testing helps characterize material behavior, essential for industries like food, polymers and pharmaceuticals
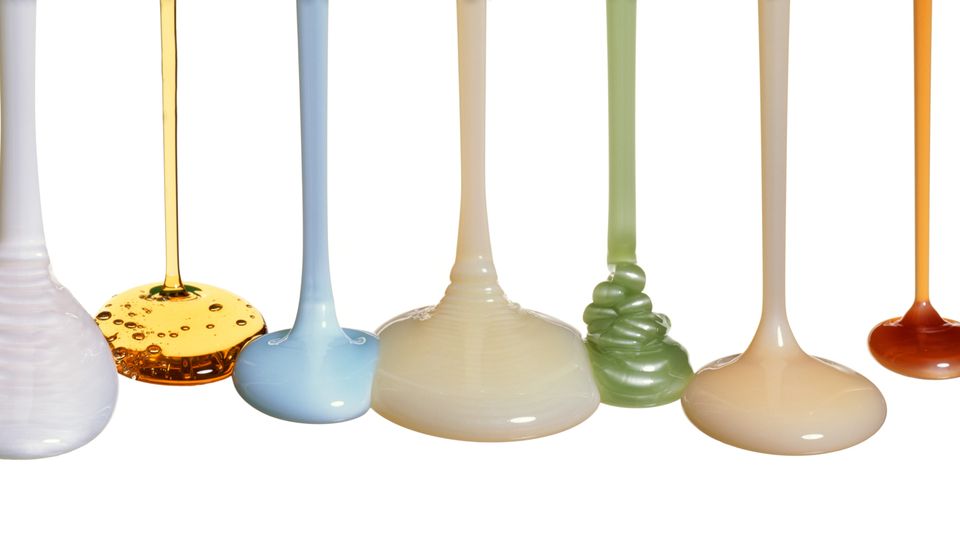
Complete the form below to unlock access to ALL audio articles.
Rheology is the study of the flow and deformation of materials under applied forces, covering both liquids and solids. It examines how materials respond to stress, strain or flow, revealing information about their viscosity, elasticity and plasticity. Rheological testing helps characterize material behavior, essential for industries like food, polymers, pharmaceuticals and coatings, ensuring optimal performance and processability in various applications.
What is rheology?
Rheology definition
What is rheology?
Rheology is the branch of physics devoted to studying how matter deforms and flows, providing valuable insights into material behavior. By examining the relationship between stress and deformation, rheology connects a material’s intrinsic properties to its overall performance.1 A key tool in this field, the rheometer, applies stress or strain to a sample and measures the resulting deformation or stress.2 Rheology explores materials through two main aspects: deformation and flow.
- Deformation refers to a material’s change in shape when subjected to a force. For instance, a rubber band temporarily alters its shape when pulled.1,3
- Flow, on the other hand, measures the displacement of a fluid from one point to another. The resistance to flow, known as viscosity, determines how easily a material moves.1,3
Rheology definition
Rheology is the scientific study of how materials deform and flow in response to applied forces, encompassing both solid-like and fluid-like behaviors, and linking these responses to the material's properties and performance.4,5
Understanding rheological properties
To understand the concepts of rheology, the two-plates model is often used to define rheological parameters (see Figure 1). Considering a sample placed between two plates of area A that are a distance of h apart, a force F is applied on the top plate, causing it to move the distance x at a constant speed V.
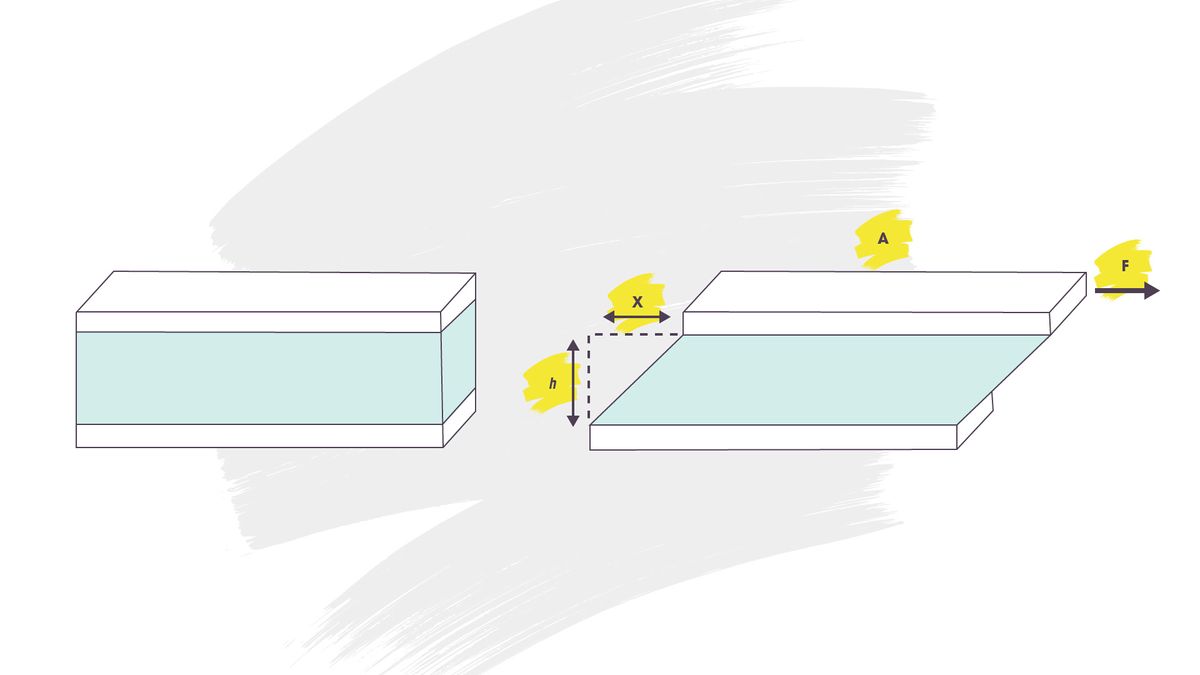
Figure 1: Two-plate model for quantification of shear rate and shear stress. Credit: Technology Networks.
- Shear flow
Shear flow can be described as layers of fluid sliding over each other, where the upper layer moves at maximum speed and the bottom layer remains stationary. In this case, when steady-state conditions are reached, the fluid undergoes a constant, uniform shear rate flow. Hence, the shear stress (𝞃) is a measure of the force per unit area applied tangentially to a material, being defined by equation 1.
Equation 1: Definition of shear stress.
The shear rate (𝞬̇) quantifies how quickly the fluid layers deform or "shear" over time, typically described as the velocity gradient perpendicular to the direction of flow, as defines in equation 2.
Equation 2: Definition of shear rate.
- Viscosity and viscous material properties
Given the above, the dynamic viscosity (η), can be defined as the coefficient of proportionality between the shear stress and shear rate, and by definition it is a quantitative measure of the internal fluid friction, related to the loss of kinetic energy in the system. Thus, viscous material properties describe how a material resists flow under applied stress due to internal friction.6 It is important to note that viscosity in all fluids is influenced by both pressure and temperature, typically increasing with rising pressure and decreasing with higher temperatures.
Viscosity definition
Viscosity is is a measure of a material's resistance to flow and quantifies the internal frictional forces between neiboring layers that are in relative motion.
- Newtonian vs non-Newtonian fluids
Newtonian fluids are often classified as fluids with an ideal flow behavior and are characterized by a linear relationship between shear stress and shear rate. This means that their viscosity remains constant regardless of changes in shear rate or shear stress. Examples of Newtonian fluids include water, simple hydrocarbons and dilute colloidal dispersions. In contrast, non-Newtonian fluids exhibit viscosity that changes based on the applied shear rate or shear stress, such as paint, ketchup or starch suspensions. Sub-classifications of non-Newtonian fluids include shear-thinning and shear thickening fluids.
- Shear-thinning and shear thickening
Shear-thinning fluids (or pseudoplastic fluids) are characterized by decreasing viscosity with increasing shear rate. Shear-thickening fluids (or dilatant fluids) suffer an increase of viscosity with the increasing shear rates.4,7 In Figure 2, it is possible to visualize the flow curves (A) and viscosity relation with shear rate (B) for the different types of fluids.
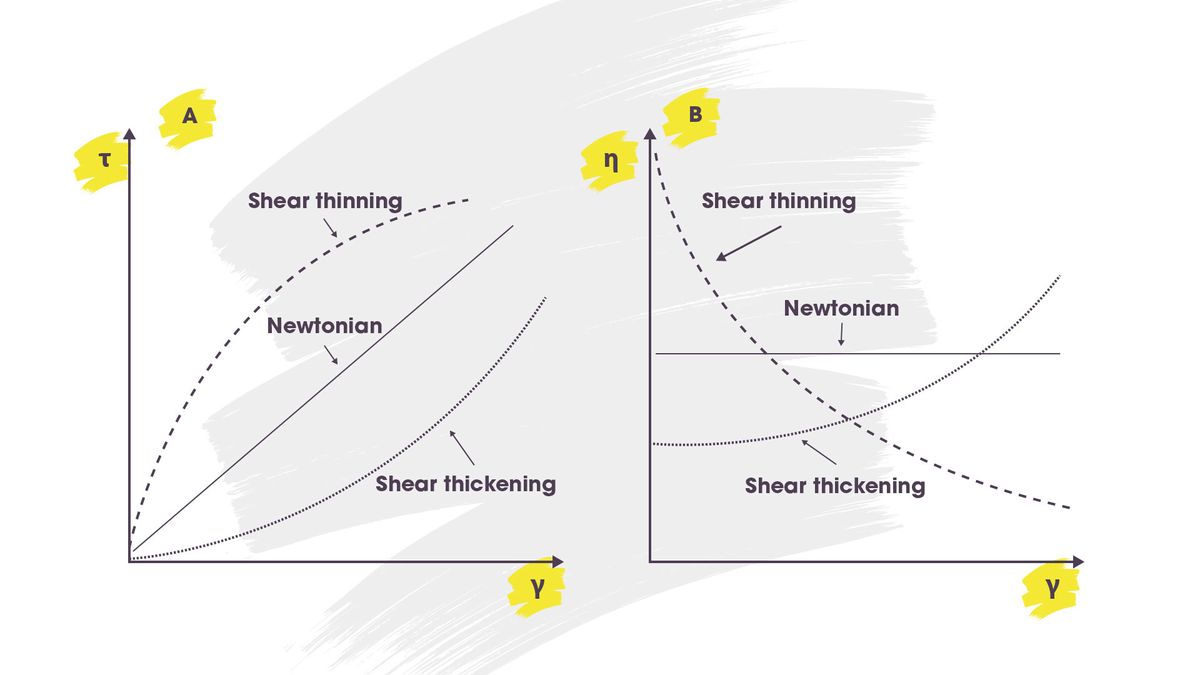
Figure 2: Flow curves (A) and viscosity curves (B) for Newtonian, shear-thinning and shear-thickening flow behavior. Credit: Technology Networks.
- Yield stress
The flow models presented previously define free-flowing fluids that flow without significant resistance when subjected to small forces. Other fluids can exhibit both solid-like and fluid-like behavior, requiring a significant force to start to flow. This force, known as yield stress, is the minimum amount of stress required to make a material flow. Below this stress, the material behaves like a solid, resisting deformation. Examples of these materials are Hershel-Bulkley and Bingham plastic materials that require a finite amount of stress to deform.8
- Elasticity, viscoelasticity and elastic deformation
More viscous materials under low stress or materials with the presence of network structures, can present solid-like characteristics associated with elasticity, being designated viscoelastic. Elasticity is the property of a material that allows it to endure stress and return to its original state after the removal of an applied force or stress. This behavior happens as the material stores energy during deformation and releases it upon recovery. In this context, elastic deformation refers to the reversible change in shape or size of a material under an applied force. This deformation is finite, and after the yield stress is overcome (the elastic limit), the elasticity is disrupted and the material flows or breaks.
Elasticity definition
Elasticity is the ability of a material to recover its original shape or size after being deformed by an external force, once the force is removed.
- Thixotropy
Another notorious property of non-Newtonian fluids is thixotropy. This phenomenon is a time-dependent decrease in viscosity upon constant stress or strain rate. It is also recoverable, since after the removal of stress, the viscosity gradually returns to its initial level.6 This time-dependent behavior is common in gels and suspensions such as paints, sauces, cosmetic creams and toothpaste. Thixotropic properties enable these products to stay stable in containers, flow upon stress, enabling easy application, and regain their solid like behavior.
Rheology testing techniques
The techniques used to measure the rheological properties of fluids or semi-solids are divided into two main types; rotary type and tube type. The accuracy and equipment costs can vary massively, from a simple glass capillary to complex and more accurate rotary equipment. Rheometers are more robust instruments, able to measure complex and dynamic rheological properties. These instruments apply and measure torque, angular velocity or angular displacements, by applying rotational or oscillatory motion, through a series of measuring geometries (Figure 3). Viscometers (rotational or tube) are often more limited devices that only measure viscosity. More information in viscosity measurements and viscometers, can be found here.
Rotational tests, usually performed with a cone plate or concentric cylinders, work by rotating the geometry over a fixed plate or in a vessel containing the sample (Figure 3). Due to the greater surface area and higher contact with the samples, concentric cylinders are most suited for low viscosity fluids. In contrast, cone plate geometries are more suited for higher viscosity samples, with the additional advantage of creating a uniform shear rate across the sample. This is achieved because the shear rate is directly proportional to the angular velocity of the rotating cone and remains constant regardless of the radial position due to the cone angle. By controlling the process via rotational speed or shear rate, it is possible to study processes that are dependent on flow velocity or volume flow rate. On the other hand, by controlling the torque or shear stress, it is possible to study force-dependent applications.2 With these measurements, it is possible to obtain the flow and viscosity curves of a fluid (see Figure 2).
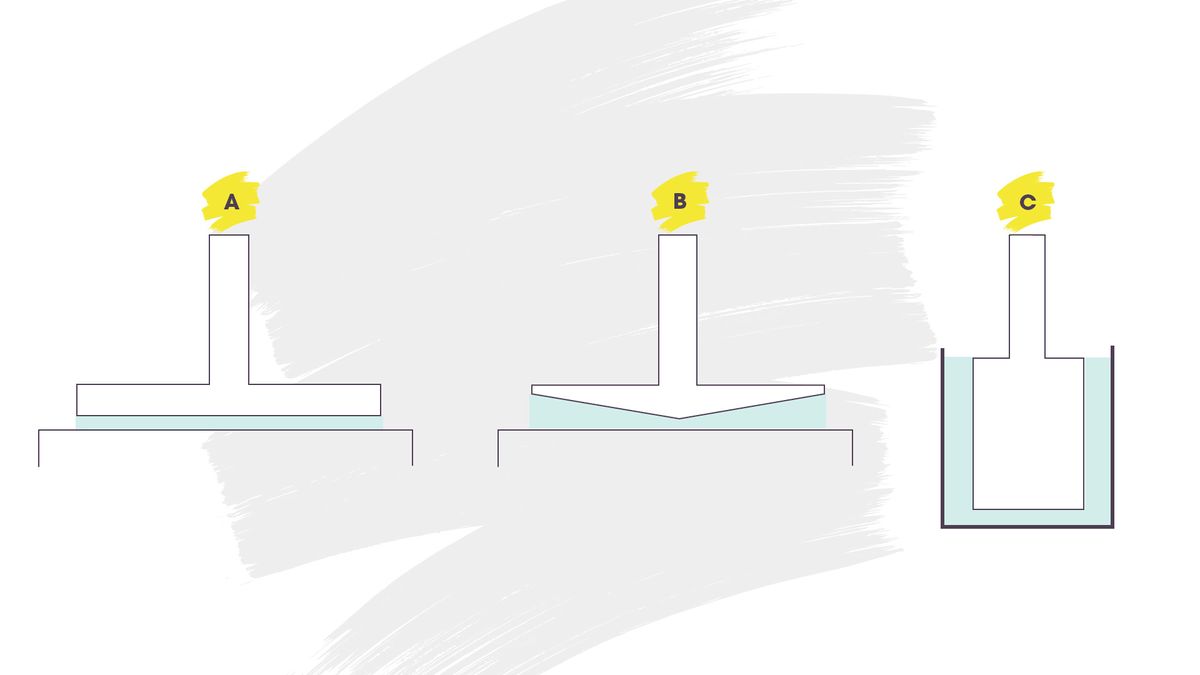
Figure 3: Examples of common rotary rheometer geometries, (A) parallel plates, (B) cone plate (C) concentric cylinders. The blue areas represent the sample being tested. Credit: Technology Networks.
Oscillatory tests are more appropriate to study the viscoelasticity of materials, where the sample oscillates around its rest position in cycles. These tests are performed using a parallel plate system with the sample loaded between the bottom static plate and the top oscillating one. The oscillatory motion can be represented as a sinusoidal wave with stress or strain amplitude on the y-axis and time on the x-axis (Figure 4).
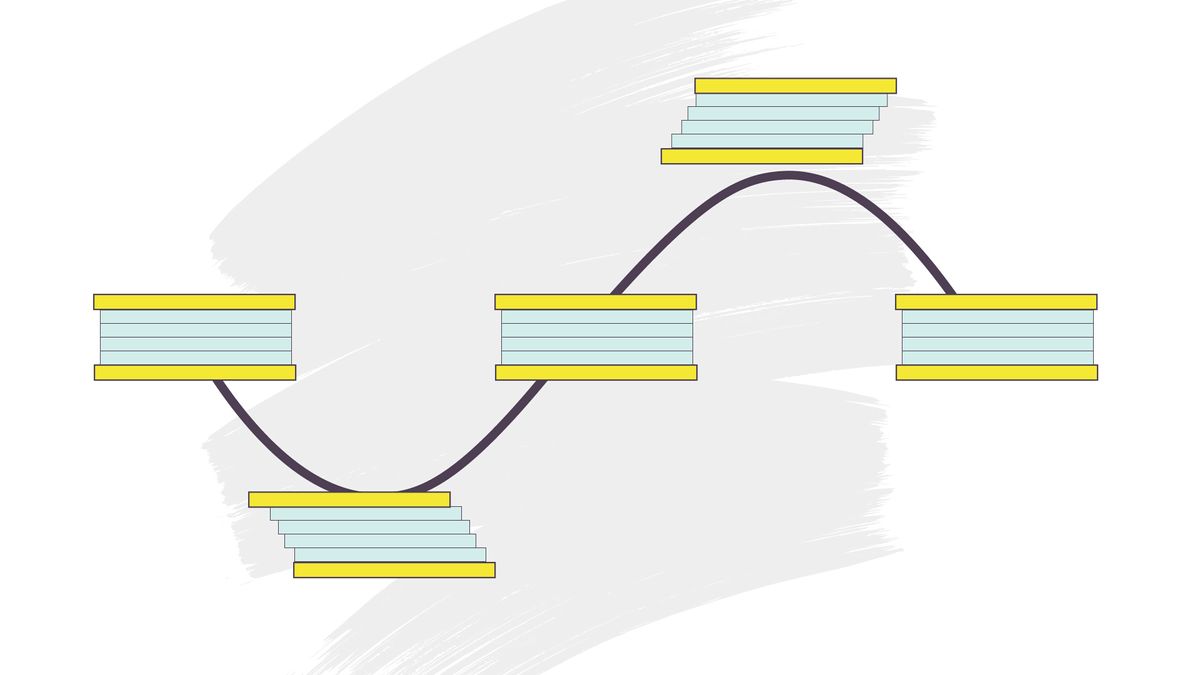
Figure 4: Illustration of an oscillatory shear profile, displaying a sinusoidal curve described by its amplitude and oscillation frequency. Credit: Technology Networks.
- Complex modulus, storage modulus and loss modulus
The ratio of applied stress to measured strain provides the complex modulus (G*), a measure of material stiffness or resistance to deformation. In a purely elastic material, stress is proportional to strain, with maximum stress occurring at maximum strain, and stress and strain are in phase. In a purely viscous material, stress is proportional to strain rate, with maximum stress at maximum strain rate, and stress and strain are out of phase by 90°. For a viscoelastic material, the phase difference between stress and strain lies between these intervals. The phase angle (tan δ) indicates the relative viscous and elastic characteristics of the material. Therefore, a viscoelastic material has a phase angle between 0° and 90°, with 45° representing the transition from solid-like to liquid-like behavior. This is often related to the gel point, where network formation or breakdown begins. The elastic component of G* is called the storage modulus (G′), as it represents energy storage, while the viscous component is called the loss modulus (G′′), as it represents energy dissipation.9 The relation between, G*, G’, G’’ and tan δ can be explained by a simple trigonometric relationship, as demonstrated in Figure 5.
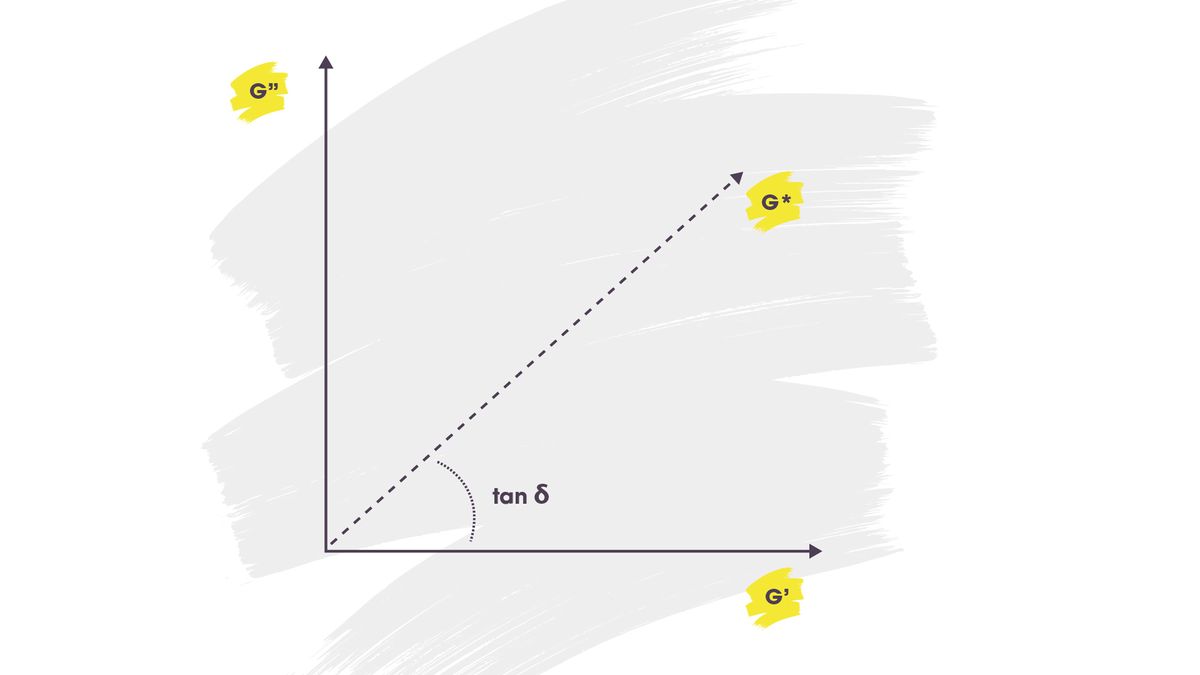
Figure 5: Geometric relationship between G*, its components G’ and G” and the phase angle tan δ. Credit: Technology Networks.
In relation to the moduli, viscoelastic solids are characterized by a higher storage modulus than loss modulus (G' > G''). This is due to a network within the material, for example chemical bonds or physical-chemical interactions. In contrast, viscoelastic liquids that exhibit a higher loss modulus than storage modulus (G'' > G') are usually characterized by weaker molecular interactions.
Extensional rheology is a less common rheological determination, measuring how materials respond when subjected to tensile force or elongation. Unlike shear rheometers, which measure the material's behavior under shear stress, extensional rheometers apply a controlled stretching or elongation to the material, typically along a single axis.10 This helps evaluate the material's resistance to stretching and its extensional viscosity. Additionally, purely extensional kinematics are challenging to control, making shear rheometers more widely used than extensional ones. A key challenge in extensional rheometry is that as the material stretches, its cross-sectional area decreases, often causing rupture before reaching steady state.
What is powder rheology?
Powder rheology refers to the study of the flow and deformation behavior of powders as bulk assemblies, consisting of solids, liquid and gas suspensions. This is a branch of rheology that focuses on interparticle interactions, such as cohesion, friction and adhesion. Different methods are combined to study powders and powder constituent mixtures, such as flow, compressibility and permeability among others.11 Among the most relevant characteristic to be determined are particle size, size distribution, shape, surface area, porosity and density. The availed methods to characterize powders and particulate materials are shear cell testing, powder rheometers, compression testing or light scattering.12,13 Powder rheology is crucial in industries dealing with powders, granules, bulk solids or suspensions. By understanding and controlling the flow behavior of powders, improvements can be made in efficiency, quality and consistency in various applications.
Rheology vs rheometry
In summary, rheology is a well-established branch of physics that started with the first observations of flow and deformation in natural phenomena, like water and honey. It evolved to an exact science with contributions from Sir Isaac Newton who established the linear relationship between shear stress and shear rate in ideal fluids and formulated the laws of motion, providing a foundation for fluid mechanics. Later, the development of elasticity theory by Robert Hooke, viscosity concepts by Jean Léonard Marie Poiseuille and the proposed model combining elasticity and viscosity finally by James Clerk Maxwell, laid the groundwork for viscoelasticity.14 Many other contributions were made to the field, such as the development of polymeric science and advances in new materials and measuring techniques.
Rheometry takes the defined principles and concepts of rheology, generating numerical data for analysis and producing measurements of rheological properties. Its outcomes allow us to obtain quantitative data on a material's flow and deformation properties. Currently, rheometry is a well-established field, with a wide range of materials characterized using various techniques across diverse linear and nonlinear deformation scenarios. However, it remains a dynamic and evolving area of research, with constant developments in measuring techniques and equipment.
Rheology modifiers and product optimization
Rheology modifiers are additives or ingredients used to adjust or modulate the flow and deformation behavior of a material, tailoring its viscosity, elasticity or thixotropic properties. They play a crucial role in product and process development and optimization across various industries by improving performance, stability and user experience through the modification of texture and sensory properties. These modifiers can be used to tune viscosity, improve stability by preventing settling or phase separation in suspensions and stabilize emulsions, dispersions or foams by modifying the material's flow behavior to resist separation. They can also be used to control specific applications, such as spreading, pumping or spraying,15 thus enabling the creation of high-performance products. Substances used as modifiers can come from a variety of origins, for example clays and minerals such as bentonite or hectorite, natural polymers such as gums, starches or modified celluloses or synthetic polymers such as polyacrylic acids, polyethylene oxide or mineral oils.16 Their versatility ensures that rheology modifiers remain a cornerstone of innovation and efficiency in manufacturing and end-use applications. Let’s consider a couple of specific examples.
- Rheology modifiers in paints
Rheology modifiers are added to paints and coatings to adjust their flow and deformation properties. Controlled viscoelastic properties ensure optimal performance during manufacturing, application and drying. They control viscosity, flow behavior and adhesion, which are crucial for ensuring a uniform and pleasing finish. In particular, they are essential to ensure storage stability, prevent sedimentation of solid components such as pigments, provide thixotropic properties that enable smooth and uniform application and allow the adjustment of viscosity for different application methods such brushing, spraying or rolling.
- Rheology modifiers in cosmetics
In cosmetics, rheology modifiers are crucial in adjusting the texture, stability and flow properties of formulations. They enable the adjustment of consistency, ensure the product is easy to apply, feels pleasing on the skin and remains stable after application. Rheology modifiers are fundamental in stabilizing emulsions, preventing phase separation, ensuring stability and uniformity by keeping insoluble ingredients like pigments or exfoliants in suspension and controlling sensory properties such as smoothness, spreadability and texture.
Applications of rheology
Rheology plays a crucial role in modern society and industrial production, influencing the design, manufacturing and performance of enumerable materials and products. By understanding how substances flow and deform, rheology connects material science and real-world applications, ensuring efficiency, quality and innovation across numerous sectors. Rheology is a vital tool for designing and optimizing product formulations and processing strategies. It plays a key role in understanding and fine-tuning microstructure and phase equilibria. Rheological studies are also crucial for defining methods of product use and application, evaluating and controlling performance, ensuring proper application and maintaining the stability and conformity of various products (Figure 6).
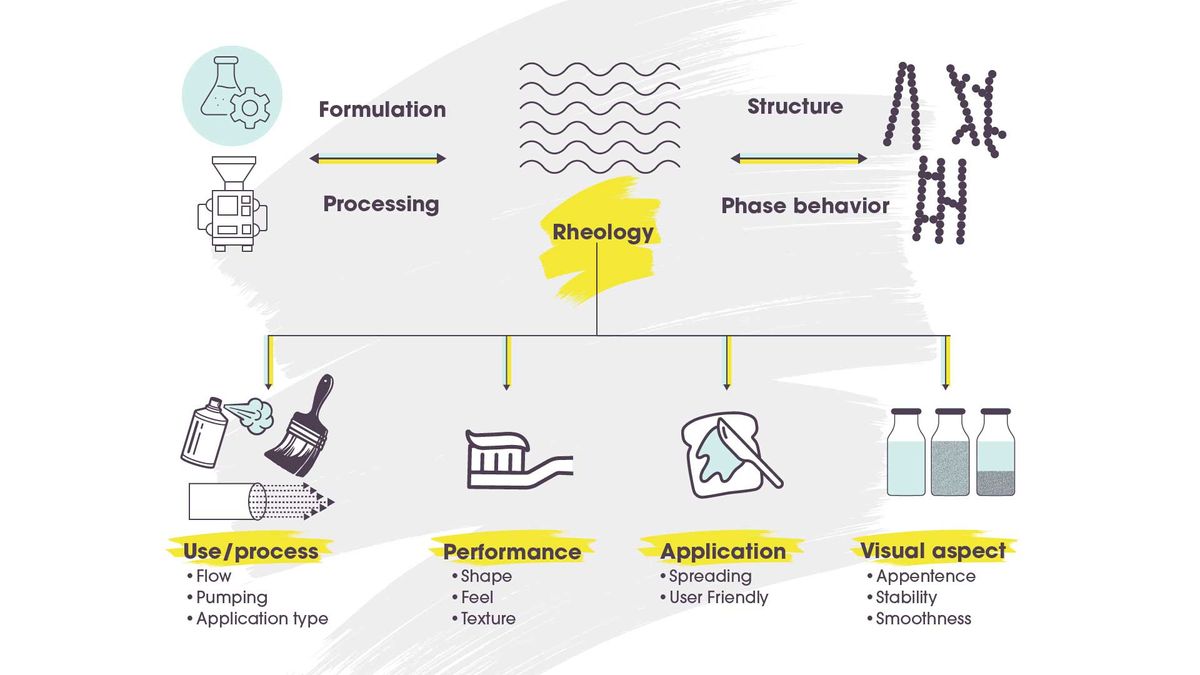
Figure 6: Schematic showing the role of rheology in product design, processes and applications. Credit: Technology Networks.
- Polymer rheology
Rheology is fundamental in polymer science, influencing every stage from material development to end-use applications. Understanding rheological properties enables advanced materials to be developed, determines how polymers melt, flow and solidify.17 It is at the foundation of processes like extrusion and injection molding, ensuring every product is strong, durable and perfectly formed. Rheology also plays a decisive role in innovative production methods such 3D printing, ensuring printability through correct viscosity, flow rate and melting behavior.18
- Food rheology
In the food sector, rheology determines texture, consistency, stability and mouthfeel, ensuring that food products meet consumer expectations.6 Its importance is widespread, from evaluation of food ingredients at all stages of the food system to food consumption, and from home cooking to the dimensioning and operation of industrial processing. Food products are diverse, ranging from simple liquids or solids to more complex matrices such emulsions, foams, suspensions, gels or multiphasic systems.19 The use of rheological measurements can help to understand and control the complex interactions between the multiple food constituents and it is fundamental in the development of new products or alternative ingredients. Particular examples are the reformulation of foods, replacing conventional ingredients with clean label ones, or the development of vegetable-based beverages and meat analogues with similar properties to animal-based products.
- Rheology in pharmacy
Rheology enables the development of new materials with particular viscoelastic properties, such as biopolymeric gels used in food products and also in medical applications such as wound care, drug delivery and tissue engineering. Also in pharmacological and cosmetic applications, rheology governs the flow of ointments that soothe, gels that deliver drugs and syrups that go down smoothly. It ensures the efficacy of injectable solutions and the correct storage and application of toothpaste or lotions, maintaining effective, safe and user-friendly products.
From polymers to pastries, pills to perfumes, rheology shapes the products we rely on every day. It is the link between science and experience, turning commodities into refined products.
1. Malkin AY, Isayev A. Introduction: Rheology: Subject and goals. In: Rheology. 3rd ed. Elsevier; 2017:1-8. doi:10.1016/B978-1-927885-21-5.50006-0
2. Grizzuti N. Rheometry. In: Reference Module in Chemistry, Molecular Sciences and Chemical Engineering. Elsevier; 2014. doi:10.1016/B978-0-12-409547-2.11007-8
3. Gallegos C. Rheology-Volume I. EOLSS Publications; 2010. ISBN:184826769X
4. Wilson DI. What is rheology? Eye. 2018;32(2):179-183. doi:10.1038/eye.2017.267
5. Struble LJ, Ji X. Rheology. In: Ramachandran VS, Beaudoin JJ eds. Handbook of Analytical Techniques in Concrete Science and Technology. Elsevier; 2001:333-367. doi:10.1016/B978-081551437-4.50012-6
6. Steffe JF. Rheological Methods in Food Process Engineering. 2nd ed. Freeman Press; 1996. ISBN:0963203614
7. Richtering W. Understanding rheology. Appl Rheol. 2002;12(5):233-233. doi:10.1515/arh-2002-0030
8. Rao MA. Flow and functional models for rheological properties of fluid foods. In: Barbosa-Canovas GV ed. Rheology of Fluid, Semisolid, and Solid Foods. Springer. 2014:27-61. doi:10.1007/978-1-4614-9230-6_2
9. Stieger M. The rheology handbook - For users of rotational and oscillatory rheometers. Appl Rheol. 2002;12(5):232. doi:10.1515/arh-2002-0029
10. Różańska S. Extensional rheology in food processing. In: Ahmed J,Basu S eds. Advances in Food Rheology and Its Applications. Elsevier; 2023:143-180. doi:10.1016/B978-0-12-823983-4.00012-1
11. Edwards SF. The rheology of powders. Rheol Acta. 1990;29(6):493-499. doi:10.1007/BF01329294
12. Mansel WB, Keen S, Patty PJ, Hemar Y, Williams MAKM. A practical review of microrheological techniques. In: Durairaj R ed. Rheology - New Concepts, Applications and Methods. InTech; 2013. doi:10.5772/53639
13. Brubaker J, Moghtadernejad S. A comprehensive review of the rheological properties of powders in pharmaceuticals. Powders. 2024;3(2):233-254. doi:10.3390/powders3020015
14. Walters K. History of rheology. In: Rheology Vol. 1. Published online 2010:91.
15. Braun DD, Rosen MR. Rheology Modifiers Handbook: Practical Use and Application. Elsevier; 2013. ISBN:0815518919
16. Tadros TF. Rheology modifiers, thickeners, and gels. In: Bröckel IU, Meier W, Wagner IG eds. Product Design and Engineering. Wiley; 2013:75-94. doi:10.1002/9783527654741.ch3
17. Kulichikhin VG, Malkin AY. The role of structure in polymer rheology. Polymers (Basel). 2022;14(6):1262. doi:10.3390/polym14061262
18. Das A, Gilmer EL, Biria S, Bortner MJ. Importance of polymer rheology on material extrusion additive manufacturing: Correlating process physics to print properties. ACS Appl Polym Mater. 2021;3(3):1218-1249. doi:10.1021/acsapm.0c01228
19. Zhong Q, Daubert CR. Food Rheology. In: Handbook of Farm, Dairy and Food Machinery Engineering. Elsevier; 2013:403-426. doi:10.1016/B978-0-12-385881-8.00015-X