Top Tips for Overcoming Plasmid Production Bottlenecks
Plasmids are critical raw materials for many advanced therapies, but going from bench to bedside can be challenging.
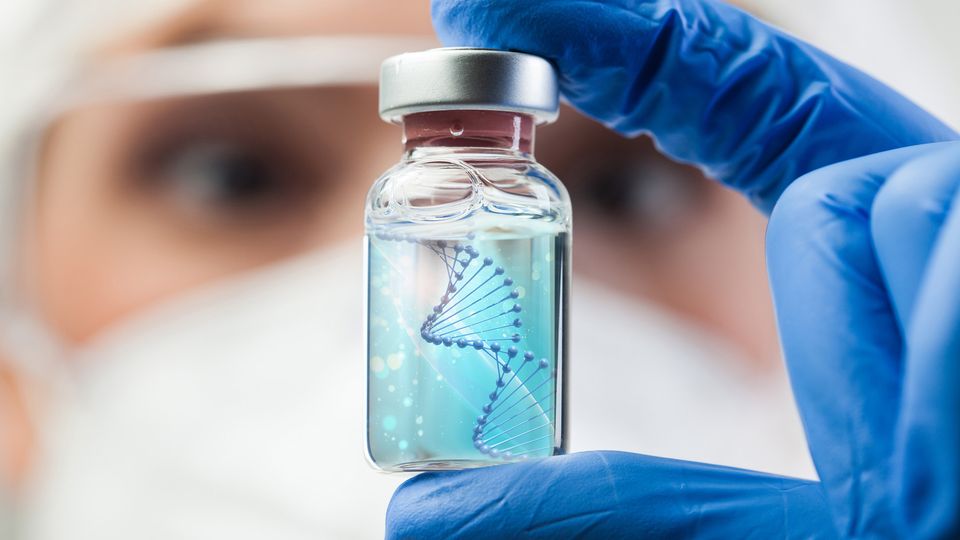
Complete the form below to unlock access to ALL audio articles.
Plasmid DNA is an essential part of cell and gene therapy products. It is utilized as a template vector for cell therapy and non-viral gene therapy and as a raw material to produce adeno-associated virus and lentiviral viral vectors, among other applications.
These genetic building blocks are often the backbone of advanced therapies; however, plasmid production comes with challenges that can halt the progress of therapies and impact their safety and efficacy.
Technology Networks spoke with Dr. John Lee, global head of cell and gene therapy at SK pharmteco to learn more about the current challenges in plasmid manufacturing and how SK pharmteco’s Precision Plasmids™ technology can help overcome plasmid production bottlenecks.
What challenges do cell and gene developers face regarding high-quality plasmid DNA production?
Developers often encounter issues with sequence liabilities, intellectual property, scalability and supplier reliability. Sequence deficiencies in plasmids, such as problematic elements that reduce yield or fidelity, often arise during good manufacturing practice (GMP) production. These can be mitigated using well-designed plasmid backbones, though these are frequently tied to suppliers with licensing fees or royalties.
Scalability is another challenge. Moving from research and development (R&D) to large-scale GMP production requires access to a robust platform and many developers struggle without one. Working with a contract development and manufacturing organization that offers proven scalability can simplify this transition.
Finally, supplier reliability is critical – developers should carefully evaluate a supplier's track record, asking questions about batch success rates, contingency plans for failures and platform robustness to ensure consistent, high-quality output. Addressing these factors early can save time, costs and resources during critical manufacturing stages.
We’ve dedicated significant effort to developing a robust, scalable plasmid platform known as “Precision Plasmids”. This platform leverages an optimized process that begins with screening various producer strains of Escherichia coli and proceeds with the evaluation of select fermentation conditions to maximize plasmid production. These steps ensure the platform can deliver high-quality plasmids at exceptional yields while maintaining scalability for GMP production.
To further enhance flexibility for customers, the platform offers two key options. Customers can insert their gene of interest (GOI) into SK pharmteco’s proprietary plasmid backbones, which are specifically designed to eliminate sequence deficiencies and optimize performance. Alternatively, our expert team can analyze and correct existing plasmids for known and cryptic sequence deficiencies. This tailored approach allows developers to meet their specific production needs while ensuring high-quality, scalable plasmid manufacturing.
SK pharmteco draws on extensive experience in plasmid development and manufacturing, gained from both supplier and customer perspectives, to address key challenges in transitioning from R&D to GMP. This expertise has informed the development of a robust platform designed to tackle common pain points.
Our proprietary plasmid backbones provide a scalable option, free from sequence deficiencies and are offered royalty-free to our customers. Additionally, our Precision Pro platform applies well-documented scientific principles to deliver consistent, high-quality plasmids with optimized yields and competitive turnaround times, ensuring a reliable solution for developers.
The guidance here is fairly straightforward – if a developer has experience with their existing plasmid-GOI combination and it has proven effective, we recommend sticking with that plasmid as they transition into the GMP space. However, if a developer approaches us with only their GOI, we encourage them to leverage our off-the-shelf destination plasmids. These plasmids are rationally designed for maximum expression in our proprietary platform, ensuring high-quality production and optimized yields.
What sets SK pharmteco apart is that our services cover the entire custom versus off-the-shelf spectrum. Developers can choose to use their preferred plasmid and our team can assist with sequence corrections or optimizations as needed. Alternatively, they can save time by selecting one of our proprietary off-the-shelf plasmids, which have been intentionally designed for superior performance. Additionally, unlike many other suppliers, we provide these off-the-shelf plasmids free of charge to customers manufacturing their GMP plasmids with us. This flexibility ensures we can meet the unique needs of each developer while simplifying the path to high-quality GMP production.
SK pharmteco is committed to reducing CoGs across all aspects of our manufacturing processes, including plasmid production, through ongoing innovation and strategic advancements. Our internal R&D team is actively exploring alternative DNA scaffolds to enhance yields, particularly for viral vector applications. This research aims to deliver higher-efficiency DNA intermediates that can directly reduce production costs while maintaining superior quality.
Additionally, we focus on continuous improvement in plasmid design and manufacturing processes. By incorporating lessons learned from ongoing operations and customer feedback, we are refining our production methods to maximize efficiency and value for our customers.
We are also leveraging our partnership with Autolomous to fully digitize our plasmid manufacturing workflow. The plan is to incorporate artificial intelligence and machine learning tools to create opportunities to optimize processes, reduce waste and improve cost-efficiency over time. These efforts will collectively ensure that SK pharmteco remains at the forefront of innovation while helping our customers lower their manufacturing costs and accelerate their therapeutic development timelines.